Direct Injection: The Fuel Technology Revolution Driving Modern Engines
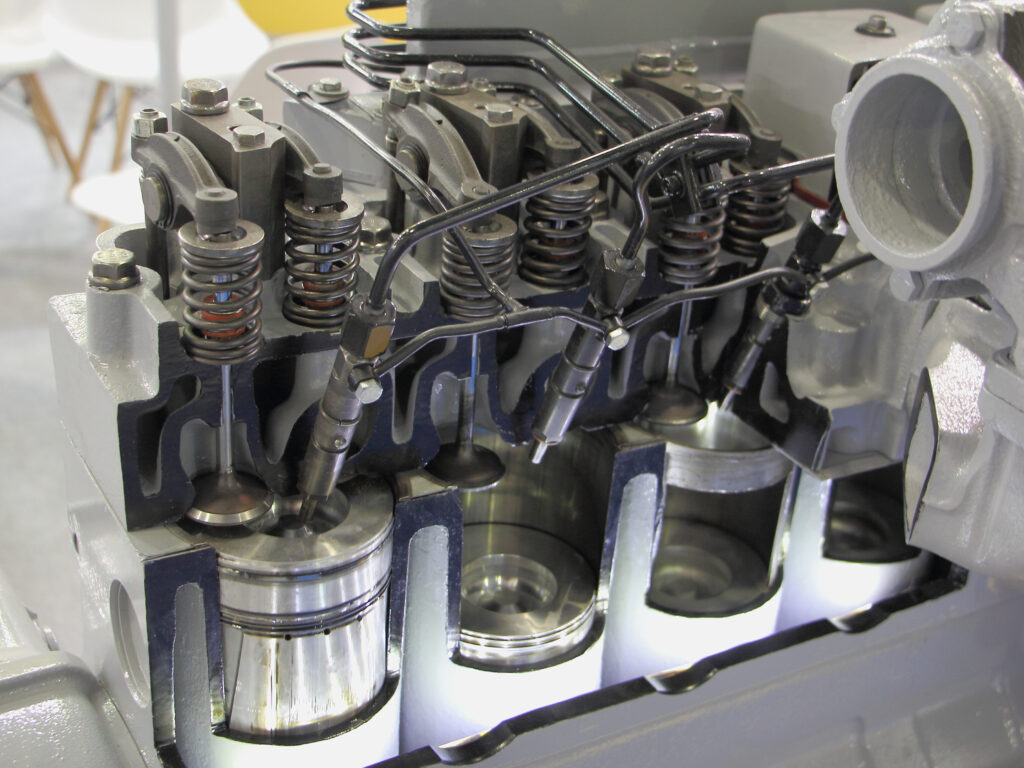
Direct injection has become a game-changer in modern automotive engineering, offering improved efficiency and performance compared to older fuel delivery systems. Unlike traditional port injection, which introduces fuel into the intake manifold before it reaches the combustion chamber, direct injection delivers fuel straight into the cylinder at high pressure. This approach provides more precise control over the air-fuel mixture, resulting in better combustion, increased power, and improved fuel economy.
Table of Contents
How Direct Injection Differs from Traditional Port Injection
In conventional port injection systems, fuel and air mix before entering the combustion chamber. While this method has been reliable for years, it lacks the precision and efficiency that direct injection offers. By injecting fuel directly into the combustion chamber, direct injection engines achieve a more complete and controlled burn, optimizing power output and reducing emissions.
Advantages of Direct Injection
One of the key benefits of direct injection is its ability to enhance fuel efficiency without compromising performance. Because fuel is delivered with pinpoint accuracy, engines can operate with leaner air-fuel ratios, reducing fuel consumption and emissions. This technology also allows for better throttle response and more torque at lower RPMs, making it ideal for performance-oriented and turbocharged applications.
Another advantage of direct injection is its ability to support higher compression ratios. With better atomization and combustion control, engines can generate more power per cycle while maintaining efficiency. Automakers have embraced this technology to downsize engines without sacrificing performance, enabling smaller engines to deliver impressive horsepower and torque comparable to larger displacement engines with port injection.
Common Challenges with Direct Injection
Despite its numerous benefits, direct injection is not without its challenges. One of the most significant issues associated with this technology is low-speed pre-ignition, or LSPI. This phenomenon occurs when fuel and oil residues combust prematurely in the cylinder, leading to engine knocking and potential damage to critical components such as pistons and connecting rods. LSPI is particularly common in turbocharged engines operating under high loads at low engine speeds.
To mitigate the risk of LSPI, manufacturers recommend using specially formulated engine oils designed to reduce deposit formation and prevent premature combustion. Following the manufacturer’s guidelines for oil changes and using high-quality fuels can also help minimize the occurrence of LSPI and maintain engine health.
Another challenge with direct injection systems is carbon buildup on intake valves. Since fuel is injected directly into the cylinder rather than passing through the intake ports, the natural cleaning effect of fuel washing over the valves is lost. Over time, carbon deposits can accumulate, restricting airflow and reducing engine performance. Some manufacturers have addressed this issue by incorporating dual-injection systems that combine both port and direct injection to help keep intake valves clean.
Maintenance Tips for Direct Injection Engines
Regular maintenance is crucial to ensuring the longevity of a direct injection engine. Periodic intake system cleaning and using top-tier fuel additives can help prevent carbon buildup and maintain optimal performance.
The Future of Direct Injection
Despite these challenges, direct injection technology continues to evolve and improve, offering drivers a combination of efficiency, power, and lower emissions. As automotive engineers develop new solutions to address its shortcomings, direct injection remains a cornerstone of modern engine design.
For car enthusiasts and daily drivers alike, direct injection provides an exciting opportunity to experience enhanced performance and fuel savings. However, understanding the maintenance requirements and potential challenges associated with this technology is key to making the most of its benefits and ensuring long-term reliability.
Want to read more articles like this?
Join the PowerNation Email NewsletterRead More from PowerNation
- Chapters
- descriptions off, selected
- captions off, selected
This is a modal window.