How To Create Your Next Engine Build Plan
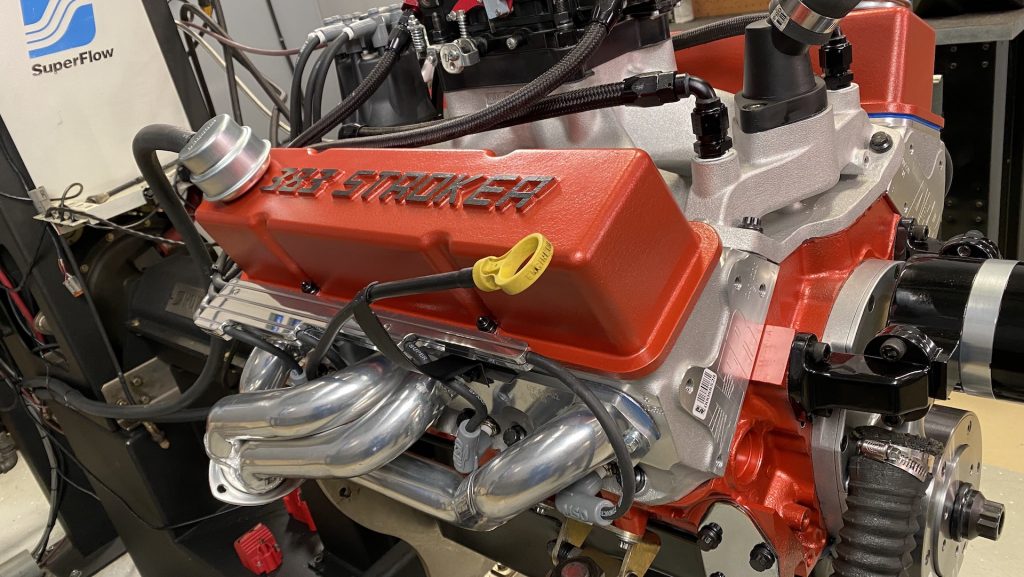
Building engines is one of the coolest things we get to do here at POWERNATION because every project starts with an engine build plan. We get to put the constructive and architectural parts of our brains to work on something that can crank out enough horsepower and torque that it can become the high-powered centerpiece of any project car. As fun and rewarding as it is, we often get asked is “How do we get started?” There are literally and figuratively so many moving parts involved in the engine building process, sometimes figuring out where to begin can feel overwhelming. That’s why it’s important to always have an engine build plan before starting every project.
To help explain the process, we are going to walk you through how we created the build plan for a recent project and the factors that we look at when starting out. We will show you how we planned the build for our pump gas street engine that needs to make 500 hp, but these are the same steps we do for every engine build, regardless of brand or size. So come along with us as we show you how we plan out our engines before any wrenches are turned!
Choosing Your Engine Platform
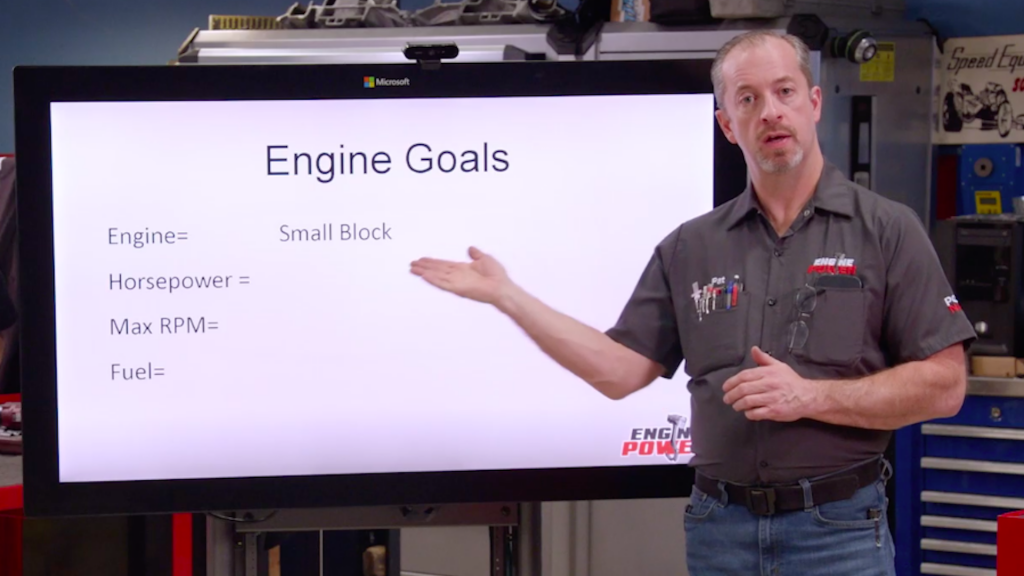
These days there are a plethora of engine options to pick from for your next project. It really comes down to a few factors like your power goal and your budget. For instance, if you already have an engine block or a complete engine, you’re one step ahead. If the power level you’re trying to achieve is out of reach or too costly for that platform however, you might want to look into swapping for an engine that is capable of producing that power, or at least doing it in a more economical fashion.
Another major limiting factor is what vehicle and application the engine is going into and the physical space and weight limits of the chassis. Depending on the project, you might not want to cut half the car apart just to fit a larger engine, so it’s something to keep in mind when picking your engine platform.
For example, in our engine build plan, we are going with an iron small block LS because they are generally inexpensive, easy to come by, can fit in a variety of applications and there are plenty of ways we can customize it.
What Is Your Horsepower Goal?
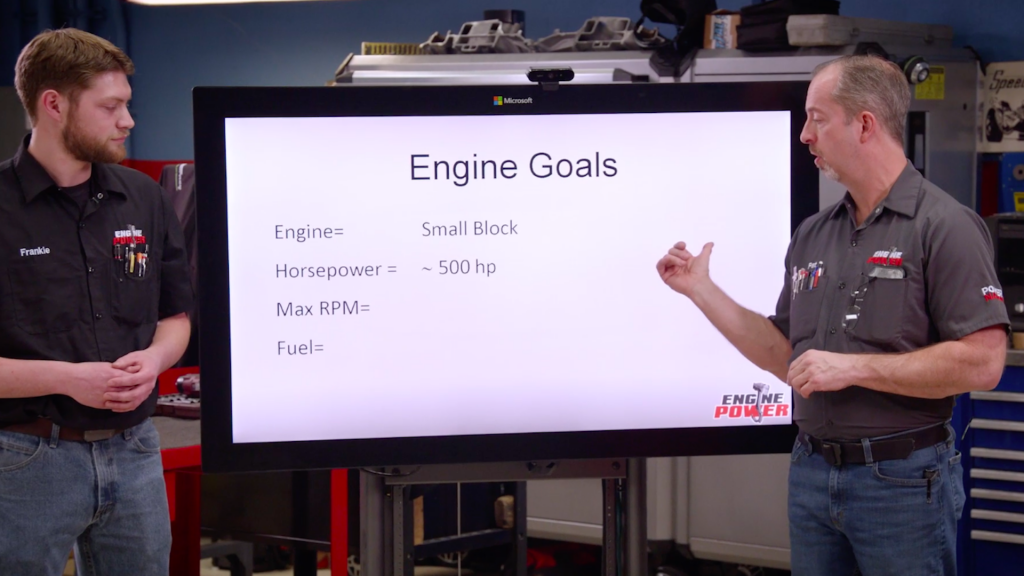
In a perfect world, we could create a small-block engine with infinite amounts of horsepower and torque. But sadly, we have to be more reasonable. In our case, we want our small block engine to be able to produce 500 horsepower. It will certainly be spicy on the street, and it’s also very possible to do, but we need the correct combination of parts to reach our goal. Thankfully for us, parts for a project like this are pretty easy to come by, and a simple bolt-on package can help us meet this goal.
Determine Your Max RPM
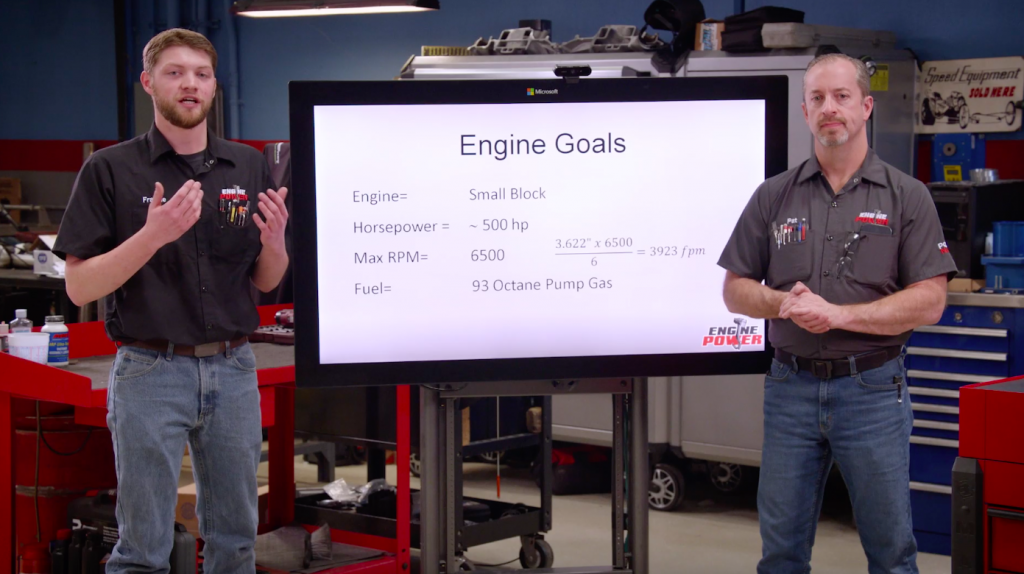
RPM make the engine world go round, and every engine build should have a maximum RPM limit that will allow it to perform safely. The more RPM that your engine turns, the pricier it is going to be in order for you to make that happen. Also, your maximum RPM should not be just some arbitrary number. It is directly related to where the engine will make peak horsepower and, depending on the application, how well power carries past that. The biggest limiting factor for RPM is the strength and quality of parts being used. If you are going to start turning a high amount of RPM, the price goes up exponentially!
For our engine build plan, we chose 6,500 RPM because we want to keep the cost of this project low. That means we are going to be using the stock crank, stock rods, and probably even the stock pistons. Since we are using stock components, we want to keep our average piston speed under 4,000 ft/min to keep the stress on the rotating and reciprocating components lower. In order to calculate our mean piston speed, we simply take our engine stroke (3.622”), multiply it by our target maximum RPM (6500), and then divide it by six. Our total will then come out to be 3,923 ft/min which is right under our limit for safety and durability.
Choose Your Fuel Type
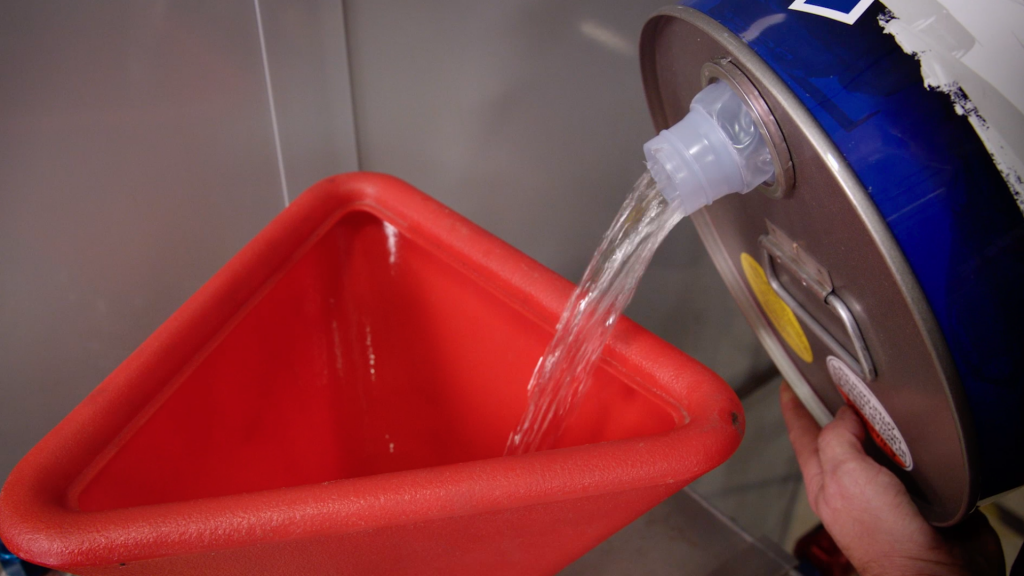
Every type of fuel has its own benefits and limits so knowing the type of fuel that you’re going to be burning in your engine is a major factor in the specific output and power it is able to produce. In most race applications, using expensive, distilled racing fuel is a given, and there are a large variety of options with several different manufacturers, octane ratings, and oxygen/lead contents. Since most of our engines are high-performance street engines, we primarily use 93 octane pump gas since it can support a good amount of cylinder pressure, is easy to get, and is relatively inexpensive compared to racing fuel.
We will be running our LS on 93-octane fuel straight out of the local pump for this application as well. Hopefully, fuel will be the most expensive thing you put in your engine once is it complete. So it’s important to look at all the options and choose the right one for your build.
Determine Your Engine Displacement
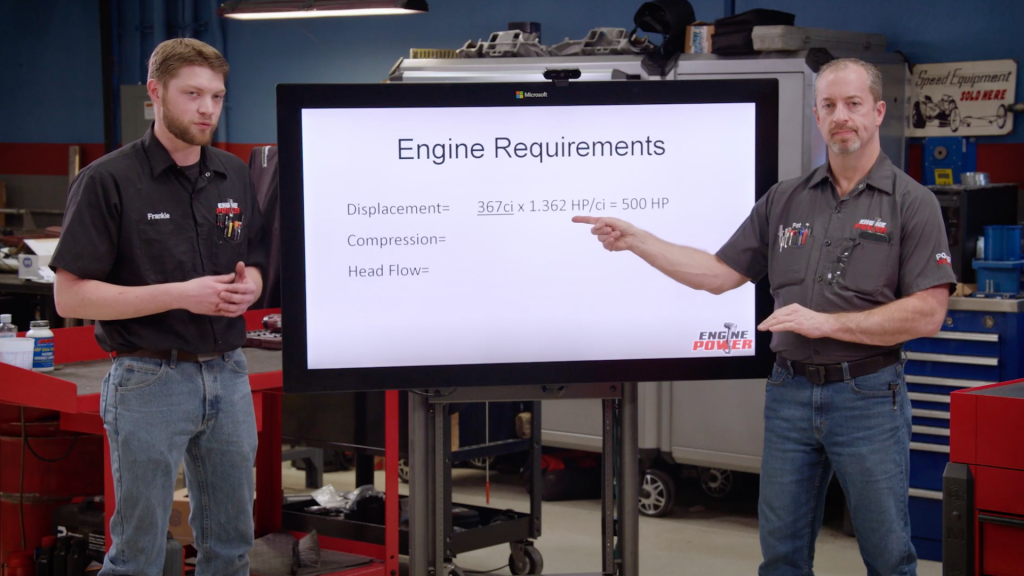
Now that we’ve determined the goals you’ve set for your engine build, the next thing on our list will be the engine’s requirements to reach those goals. Specs like: How many cubic inches does it have? How much horsepower per cubic inch will you need in order to reach your overall horsepower goal? If the specific output needed is beyond what is capable on the fuel you’re using or the budget for your engine, you might have to look into building a stroker out of your engine or picking a platform with a higher displacement.
Our 6.0L LS is 367 cubic inches and, to make our 500hp goal, would need to produce a specific output of 1.362 hp/ci. That is definitely achievable in our application, so we don’t need to worry about increasing the displacement for this build.
Calculate Your Compression Ratio
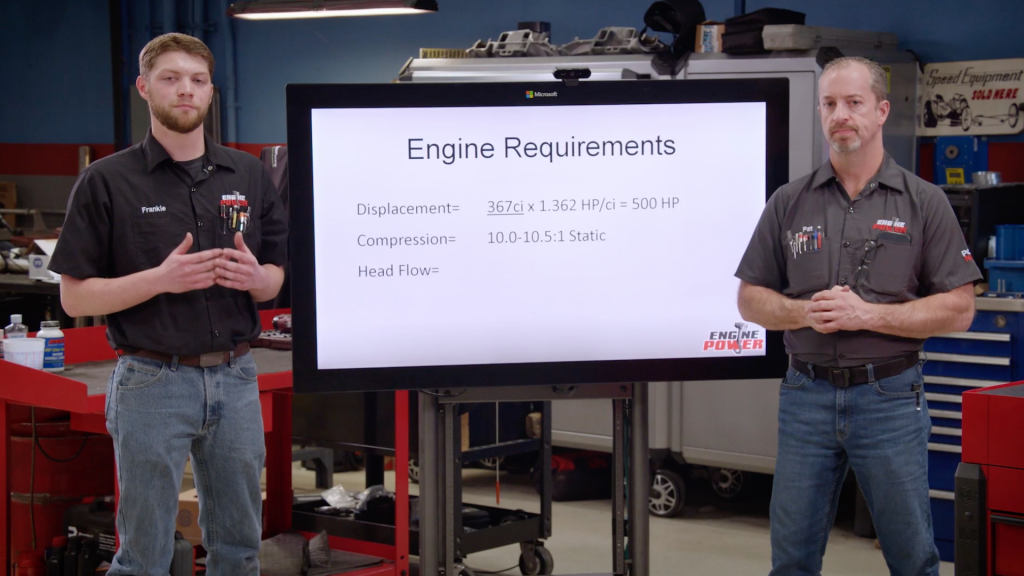
Once you’ve figured out your displacement, you will next have to determine how much compression you will need in order to effectively burn fuel and produce your power goal. In high-performance applications, this is usually limited by the octane of the fuel being used, and having a higher compression ratio narrows the tuning window, making it much easier to put the engine into fatal detonation if the tune-up is pushed too hard.
The “limit” on compression varies depending on the application but for 93 octane pump gas, we generally find the safe limit is between a 10.5:1 and 11.0:1 static compression ratio. For this build, based on previous builds and data, we are going to need between 10.0:1 and 10.5:1 to reach our target horsepower number, and our 6.0L has a 10.1:1 static compression ratio stock. Perfect!
How Much Cylinder Head Flow Do You Need?
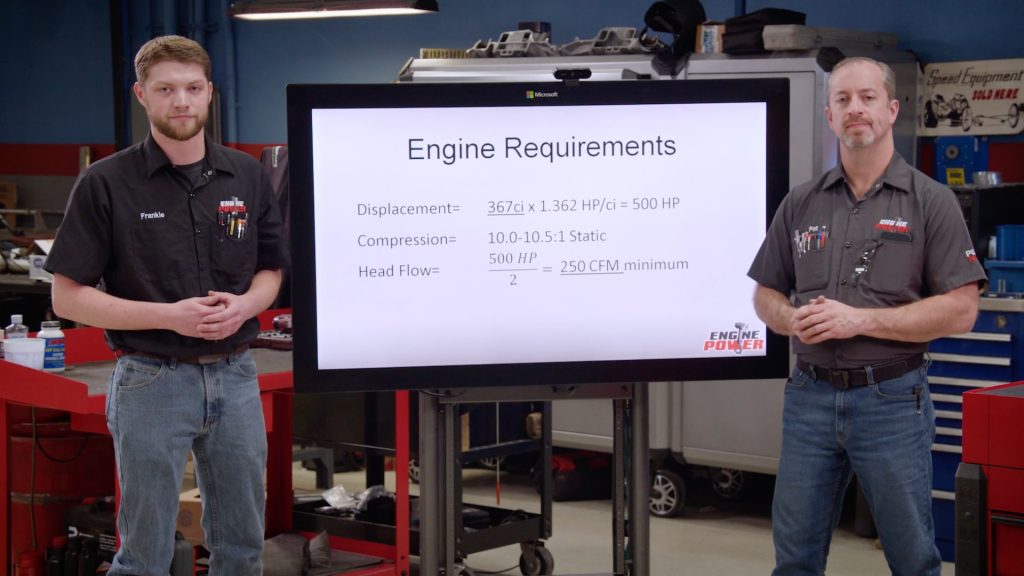
This is a crucial part of every engine build because having the incorrect induction package can cause your project to fall short of its horsepower goal. If your engine isn’t getting enough air and fuel flowing, don’t be surprised if it isn’t generating as much power as you were expecting. Thankfully, there is a simple math formula to help determine the minimum amount of airflow in your cylinder heads needed to meet your target. The industry standard is that you can make 2 horsepower per CFM (cubic feet per minute) of peak head flow.
Using our application, our goal is 500 horsepower. After we divide that by two, we are left with 250 CFM of head flow. The stock 317 casting cathedral port heads on our LS flow 255 CFM, which is as much as some aftermarket old-school Chevy heads and will be a great fit for this build without any porting.
Choose Your Intake Manifold
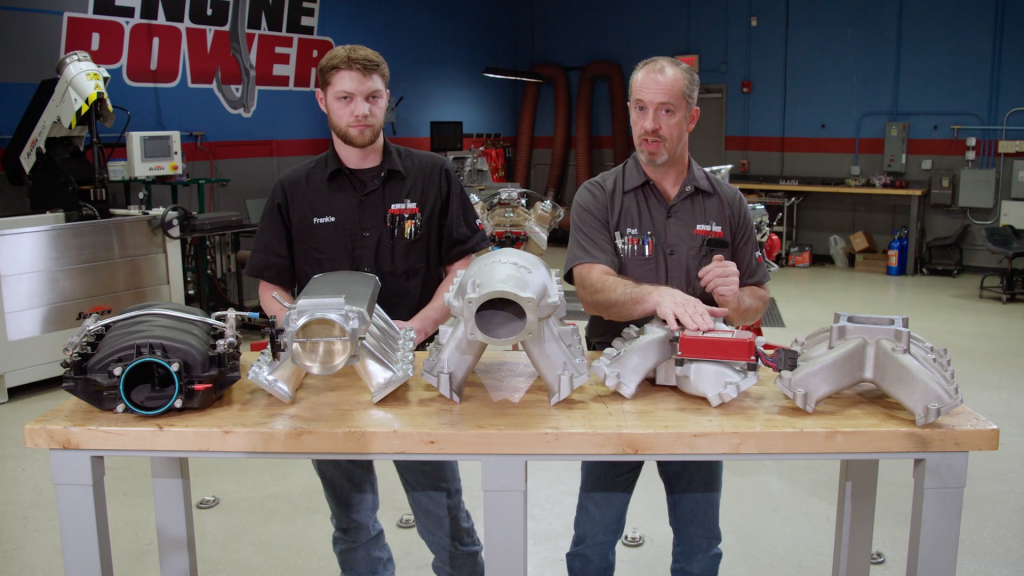
A piece that needs to be well-matched to the cylinder heads and can have a measurable impact on not only how much power an engine makes, but where it makes it is the intake manifold. An intake should complement the cylinder head, meaning you don’t want one that is drastically larger or too restrictive for the intake port. There are several different styles and types, from fuel-injected vs. carbureted, single plane vs. dual plane, and short to tall.
Barring any height constraints in the vehicle, you should pick the intake that is best suited to your application, has an intake tract that will be sized correctly for the cylinder head, and has the correct length for the RPM you plan to run. On our 6.0L LS, we are going to be running a simple but effective carbureted single-plane Victor Jr. with a stand-alone ignition controller.
Final Thoughts
These are all important factors when planning out your engine build, and although we went through them in order, there are several that are connected and must be considered at the same time. These are how we start every engine build and can get you started on planning your next engine build as well.
While all the math looks good on paper, the next step in our process is the fun part… actually building the engine. Once we bolt on every last part of our build, we get to verify our results and put them to the test in the dyno cell. If the numbers come out to what we predicted, then we’ve got a successful engine build under our belt!