GM Has Opened The First Major 3D Printing Facility For Production Car Parts
If you purchase a General Motors vehicle in the future, the parts could very well be 3D printed.
The automaker announced today a new facility dedicated to additive manufacturing has officially opened. Now, GM engineers will have access to an entire branch that is exclusively dedicated to producing 3D printing technology in the automotive industry. This will not only speed up vehicle development but also significantly cut down on the costs required to design a new car.
“The core component of GM’s transformation is becoming a more agile, innovative company, and 3D printing will play a critical role in that mission,” said Audley Brown, GM director of Additive Design and Materials Engineering. “Compared to traditional processes, 3D printing can produce parts in a matter of days versus weeks or months at a significantly lower cost.”
The 15,000-square-foot comprehensive facility includes 24 3D printers, which create polymer and metal solutions. GM’s additive design and manufacturing team leverages a number of processes at the AIC, including selective laser sintering, selective laser melting, Multi-Jet Fusion, and fused deposition modeling.
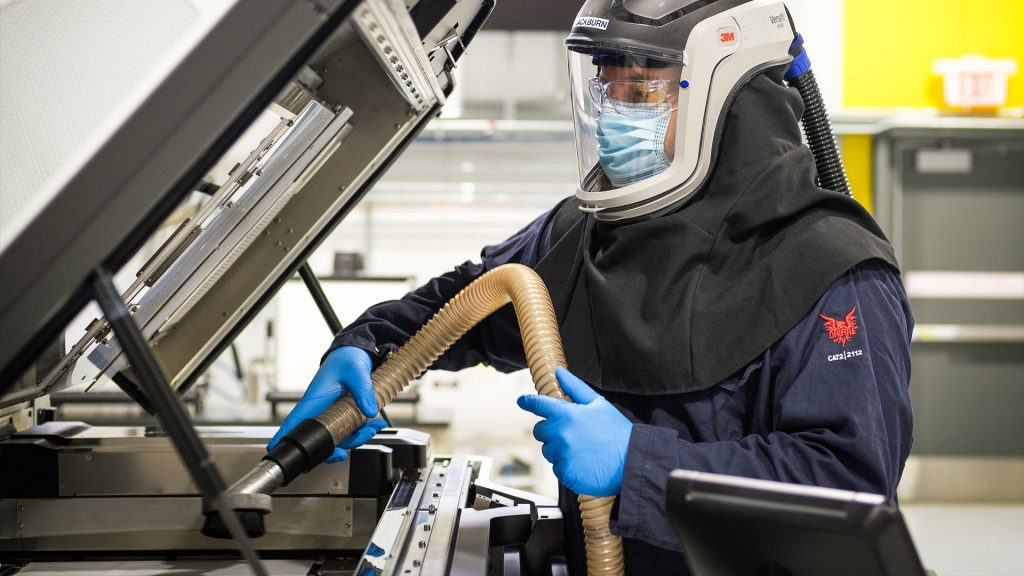
This equipment has enabled GM to produce a variety of parts which will be used in pre-production cars, at body shops, and a few vehicles that the automaker actively races such as the Corvette C8.R and Silverado race truck.
“GM is increasingly applying the benefits of 3D printing, from prototype development to manufacturing tooling and production vehicles,” said Ron Daul, GM director of Additive Manufacturing and Polymer Centers. “With the opening of the AIC, we’ll continue to accelerate adoption of this technology across the organization.”
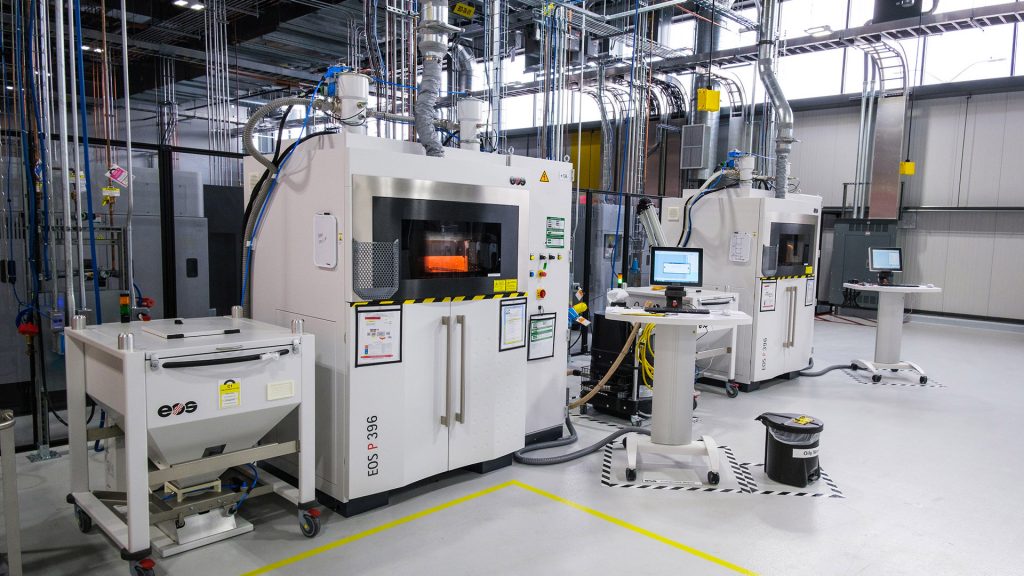
Using 3D printing functional prototypes can help eliminate expensive early tooling costs meaning engineers have the ability to iterate quickly, make design changes, and reduce development times. For example, the team 3D printed the brake cooling ducts used for the development of the Chevrolet Corvette. The 3D-printed ducts saved nine weeks of development and reduced costs by over 60 percent in the process. GM is also producing a significant number of 3D-printed tools used for assembling vehicles.
For the launch of GM’s all-new full-size SUVs, the team 3D printed nearly 100 hand tools for the body shop at Arlington Assembly. Typically, these tools would be made of aluminum and weigh anywhere from 10 to 40 pounds. The new designs, constructed with a nylon carbon fiber composite, weigh as little as three pounds and essentially eliminated the lead time for ordering part changes.
The medallion on the top of the shifter of the upcoming Cadillac CT4-V and CT5-V Blackwing’s manual transmission, along with HVAC ducts and a bracket for an electrical connector will actually be the very first production cars in GM’s lineup housing 3D printed components.
What does this mean for future production? Well, GM plans to expand its 3D printing capabilities to allow for more niche applications such as classic cars or personalized applications. Looks like 3D is the way of the future.